Porosity in Welding: Identifying Common Issues and Implementing Best Practices for Avoidance
Porosity in welding is a prevalent concern that commonly goes unnoticed until it causes substantial issues with the stability of welds. This common defect can endanger the stamina and sturdiness of welded frameworks, presenting security risks and bring about expensive rework. By comprehending the root creates of porosity and carrying out effective avoidance techniques, welders can considerably improve the high quality and reliability of their welds. In this conversation, we will explore the crucial elements adding to porosity formation, analyze its damaging effects on weld efficiency, and talk about the very best methods that can be taken on to lessen porosity occurrence in welding procedures.
Typical Reasons of Porosity
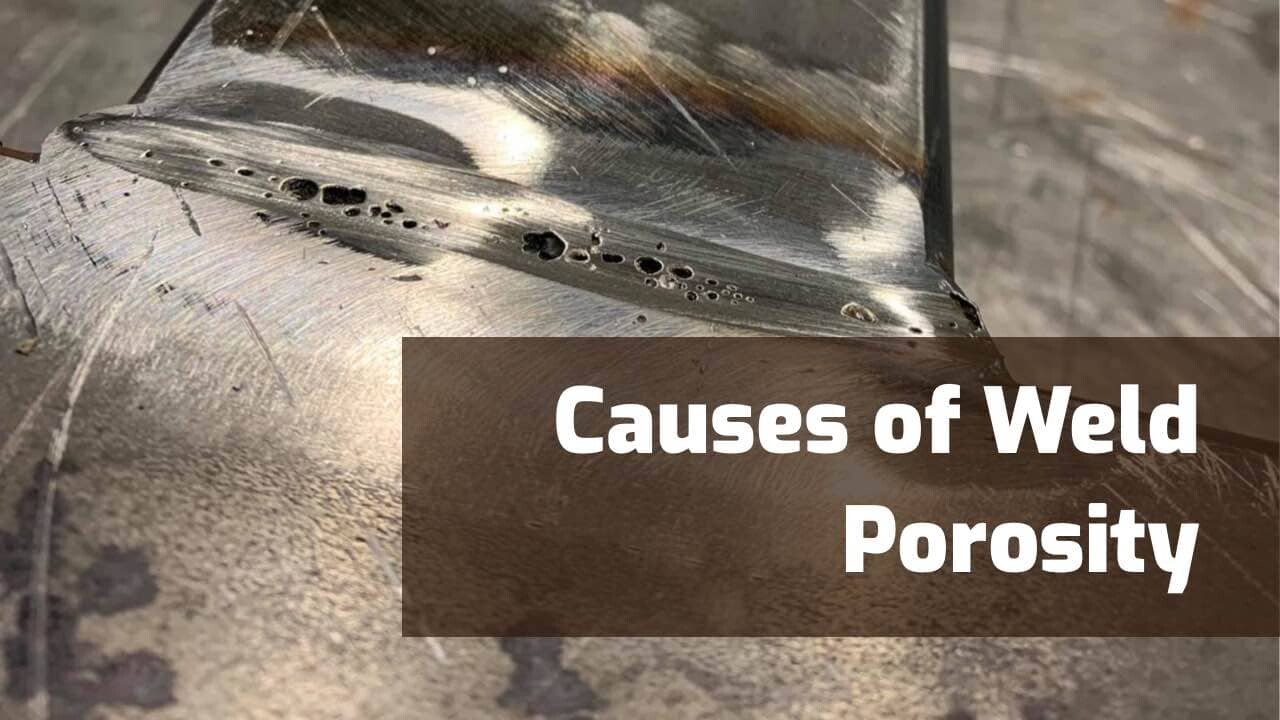
Using dirty or damp filler products can present contaminations into the weld, contributing to porosity concerns. To alleviate these common reasons of porosity, detailed cleaning of base metals, appropriate protecting gas option, and adherence to ideal welding parameters are essential techniques in accomplishing high-quality, porosity-free welds.
Influence of Porosity on Weld Quality

The existence of porosity in welding can dramatically compromise the architectural honesty and mechanical residential or commercial properties of bonded joints. Porosity develops voids within the weld metal, deteriorating its total strength and load-bearing capacity.
Welds with high porosity degrees have a tendency to display lower impact strength and lowered capacity to flaw plastically before fracturing. Porosity can hinder the weld's ability to effectively transmit pressures, leading to early weld failure and potential safety and security threats in important frameworks.
Best Practices for Porosity Prevention
To boost the architectural stability and quality of bonded joints, what certain procedures can be executed to minimize the event of porosity during the welding process? Porosity avoidance in welding is important to guarantee the integrity and toughness of the final weld. One reliable method is proper cleansing of the base metal, removing any kind of pollutants such as rust, oil, paint, or dampness that might lead to gas entrapment. Making certain that the welding devices is in excellent condition, with tidy consumables and suitable gas circulation rates, can additionally substantially reduce porosity. In addition, maintaining a secure arc and controlling the welding criteria, such as voltage, current, and YOURURL.com take a trip speed, assists develop a constant weld swimming pool that lessens the threat of gas entrapment. Utilizing the proper welding method for the details material being bonded, such as readjusting the welding angle and gun placement, can further stop porosity. Regular assessment of welds and prompt remediation of any type of concerns identified throughout the welding procedure are important techniques to prevent porosity and create high-grade welds.
Value of Correct Welding Strategies
Implementing correct welding methods is paramount in making certain the architectural integrity and top quality of welded joints, constructing upon the foundation of reliable porosity avoidance actions. Excessive warmth can lead to boosted porosity due to the entrapment of gases in the this weld pool. In addition, making use of the proper welding criteria, such as voltage, existing, and travel speed, is important for accomplishing audio welds with very little porosity.
Moreover, the option of welding procedure, whether it be MIG, TIG, or stick welding, need to line up with the details requirements of the project to guarantee optimal outcomes. Proper cleaning and preparation of the base steel, in addition to picking the ideal filler material, are also important elements of competent welding methods. By sticking to these ideal techniques, welders can decrease the danger of porosity development and produce high-grade, structurally sound welds.

Evaluating and Top Quality Control Measures
Testing treatments are essential to spot and avoid porosity in welding, guaranteeing the stamina and sturdiness of the last product. Non-destructive testing methods such as ultrasonic testing, radiographic screening, and aesthetic examination are generally used to determine prospective problems like porosity.
Performing pre-weld and post-weld evaluations is also critical in keeping quality assurance standards. Pre-weld examinations include verifying the products, devices settings, and sanitation of the work location to stop contamination. Post-weld evaluations, on the various other hand, examine the final weld for any type of problems, consisting of porosity, and verify that it fulfills specified criteria. Carrying out a comprehensive top quality control plan that consists of comprehensive screening procedures and examinations is extremely important to decreasing porosity concerns and guaranteeing the total quality of bonded joints.
Verdict
Finally, porosity in welding can be a typical issue that affects the high quality of welds. By determining the usual reasons for porosity and executing have a peek at these guys ideal methods for prevention, such as appropriate welding methods and screening procedures, welders can guarantee excellent quality and trustworthy welds. It is necessary to prioritize prevention approaches to reduce the incident of porosity and preserve the honesty of welded frameworks.